Preventing Envelope Failures
Common Envelope Failures and How to Prevent Them
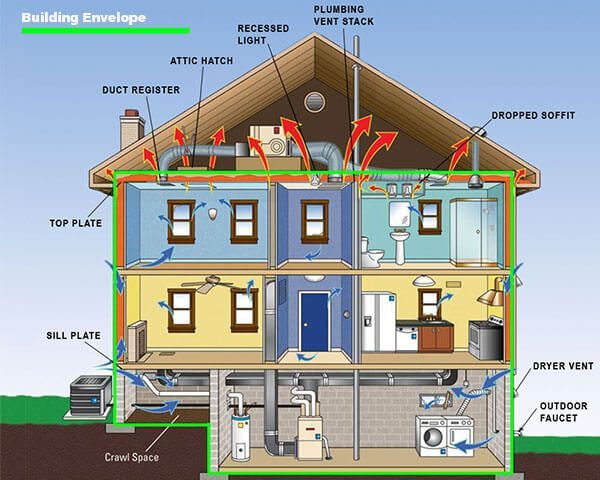
The Silent Threat to Building Performance
A building envelope is more than just walls and a roof. It’s a system designed to manage air, water, heat, and vapor flow. When even one part of that system fails, the entire structure can suffer. These failures often go unnoticed until the damage is extensive, costly, and sometimes hazardous to health and safety.
What Is the Building Envelope?
The building envelope includes all components that separate the indoors from the outdoors: walls, roofs, windows, doors, insulation, vapor barriers, and air barriers. Its job is to maintain comfort, energy efficiency, and structural integrity. When functioning correctly, it resists external forces and keeps internal conditions stable.
Common Envelope Failures
Understanding where things go wrong is the first step to preventing long-term damage.
- Water Intrusion
The most common and most damaging envelope failure. Leaks often occur due to improper flashing, poor waterproofing, clogged gutters, or failed sealants. Over time, this leads to mold, rot, and structural compromise. - Air Leakage
Gaps in the building envelope allow uncontrolled air movement, leading to energy loss, moisture transport, and comfort issues. This is especially problematic around windows, doors, electrical outlets, and joints between dissimilar materials. - Thermal Bridging
When conductive materials like steel or wood bypass insulation, heat transfers easily through the envelope. This causes cold spots, condensation, and higher energy bills. - Condensation and Vapor Drive
When warm, moist indoor air comes into contact with cooler surfaces inside the wall assembly, condensation can form. Without proper vapor control, this moisture leads to mold and degradation. - Improper Flashing and Drainage
Flashing and drainage planes that are incorrectly installed or omitted altogether fail to direct water away from critical joints and seams, particularly at windows, doors, and roof-wall connections. - Degraded or Incompatible Materials
Over time, materials can break down due to UV exposure, moisture, or incompatible chemical interactions. Sealants and membranes may lose adhesion or become brittle if not properly chosen or maintained.
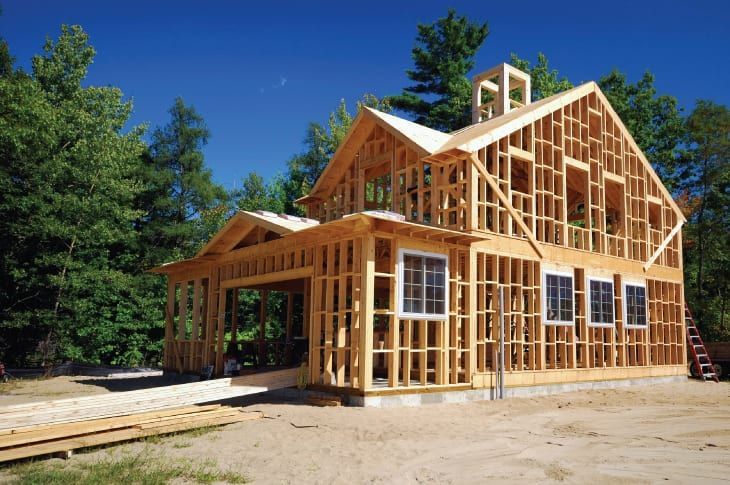
How to Prevent Envelope Failures
Prevention requires a combination of smart design, proper installation, and routine inspection.
- Design with Integration in Mind
Ensure the envelope system is designed holistically, with all layers (air, vapor, thermal, and water) working in harmony. Transitions between materials should be continuous and clearly detailed. - Use High-Quality Materials
Choose materials appropriate for the climate and exposure conditions. Invest in tested and approved products that are durable, compatible, and certified for long-term performance. - Ensure Proper Installation
Skilled labor is critical. Installers must follow manufacturer instructions and architectural details. Misaligned barriers, gaps, or shortcuts during application often cause failures. - Incorporate Redundancy
Use backup systems like drainage planes behind cladding and secondary flashings to catch water that penetrates the first line of defense. - Conduct Regular Maintenance
Inspect joints, seals, flashing, and finishes annually. Replace deteriorated sealants and address small issues before they become large problems. - Test and Verify Performance
Use blower door testing, infrared thermography, and moisture meters during and after construction to validate airtightness and thermal continuity.
Building envelope failures are avoidable, but only with foresight and care. Investing time and resources into proper detailing, material selection, and ongoing inspection pays off in comfort, energy savings, and structural longevity. By understanding the weak points and addressing them early, you can ensure your building stays resilient against time and weather.
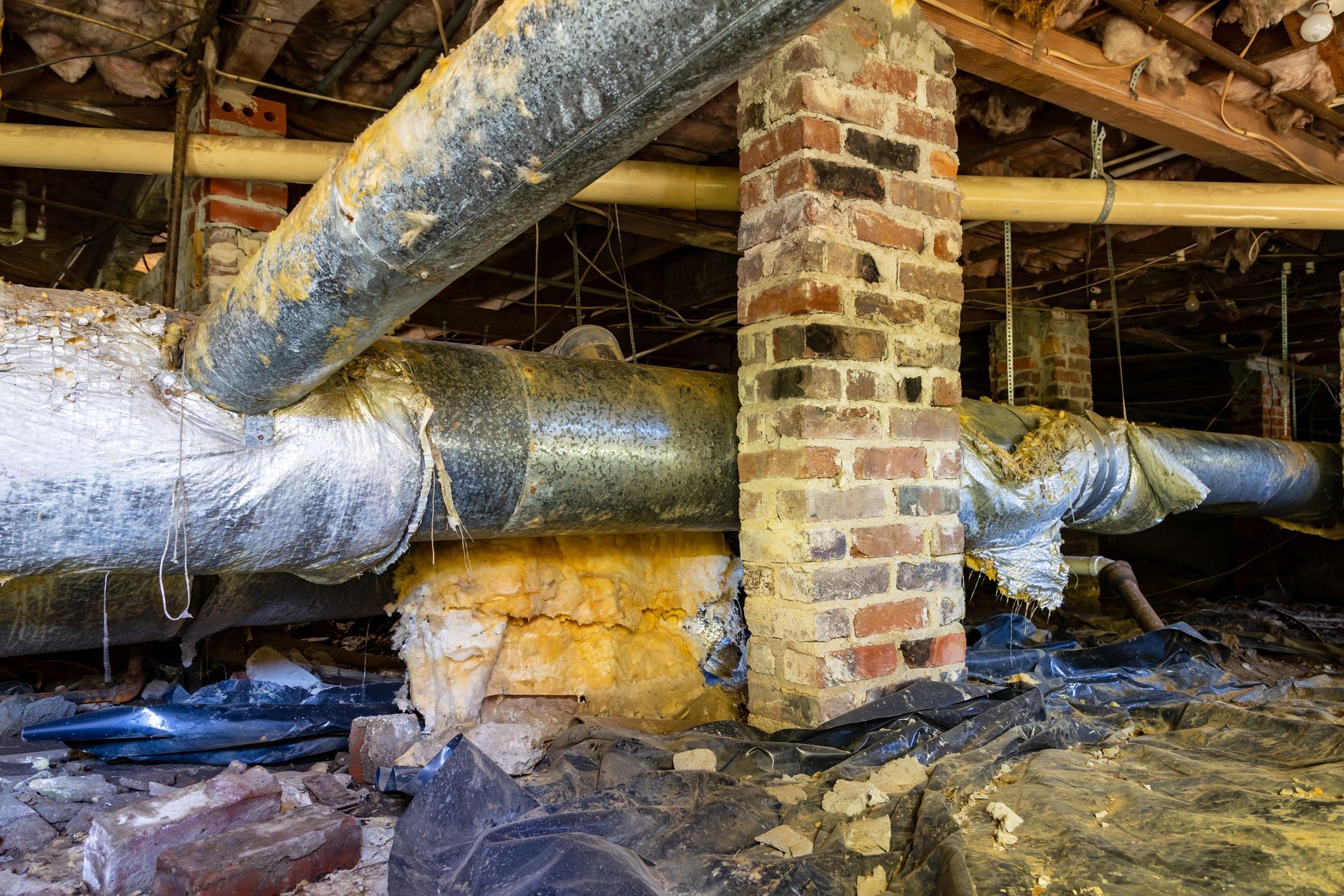
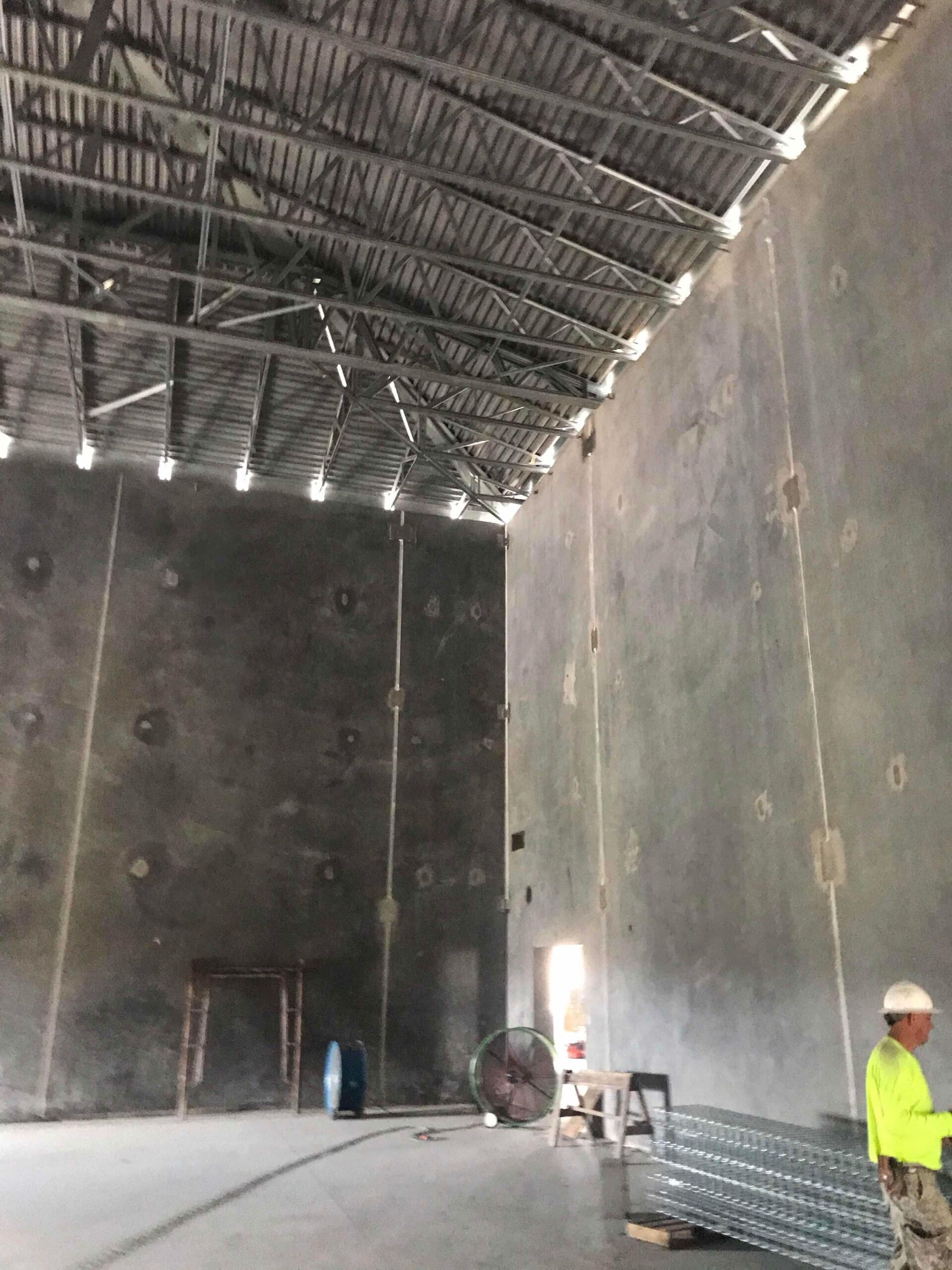